The axle is the most core set of parts and components on a semi trailer, which is directly related to the vehicle’s carrying capacity, braking effect and driving performance. If there is a problem with the axle, the vehicle’s safety, attendance rate and economic benefits will become empty talk.
Therefore, it is particularly important to do a good job of installing and repairing the axle.
Regarding the position of the axle, I believe that many car owners can still distinguish it. It is the axle that connects the wheels at both ends of the vehicle.
The axle is a light axis, and the axle is based on the axle, and the brake base plate, spherical bearing seat, air chamber seat, etc. are welded to form the axle assembly. Then, on the basis of the axle assembly, the camshaft assembly, brake assembly, wheel end assembly, cotter pin, adjustment arm, ABS sensor, ABS positioning clamp and other parts are installed, which together constitute the axle. Therefore, the axle can also be called the axle assembly.
The correct installation method and regular maintenance of the axle can keep the vehicle working condition in good condition, and the vehicle performance and safety are more guaranteed.
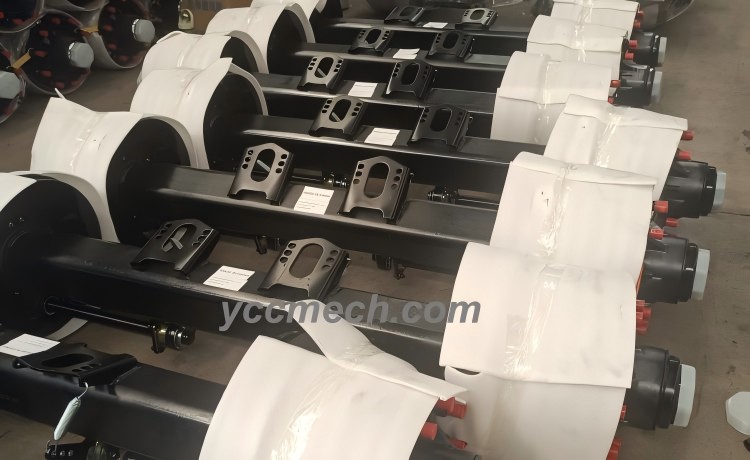
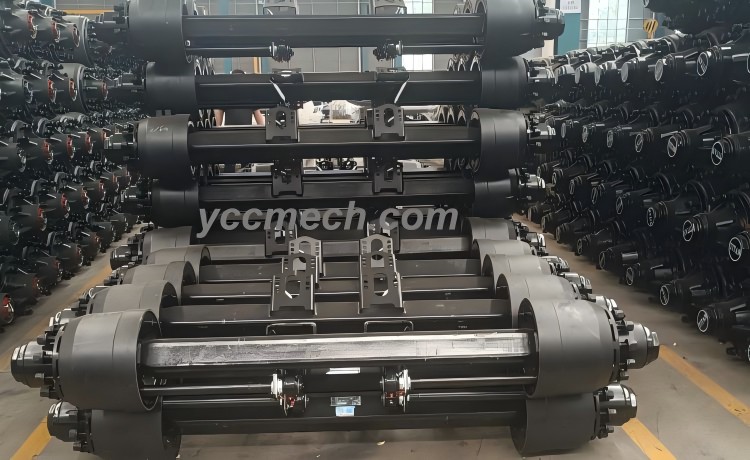
Below we will take the American type axle as an example to explain the installation and maintenance knowledge of the axle in detail.
Installation of American axle
Welding of leaf spring seat and axle:
The leaf spring seat is the place where the axle is subjected to the greatest bending stress, so the welding requirements for the leaf spring seat and the axle are very strict, and the welding quality will directly affect the service life of the axle.
The following points should be noted when welding the leaf spring seat and the axle body:
1. Whether the leaf spring seat and the axle body are in place, if not, they need to be corrected before proceeding.
2. The position of the leaf spring seat on the axle body should meet the positioning center distance requirements.
3. The welding ground wire can only be connected to the axle body, and it is not allowed to be grounded through the wheel rotating parts to avoid damage to the bearing due to over-electricity and sparking.
4. There are different welding schemes for square shafts and round shafts.
Tightening of axle bolts:
After each tire change, the nuts need to be tightened to the specified value with a torque wrench in the specified nut tightening sequence.
For JIS bolts, the spherical nut of the wheel should be removed first, and the cup nut should be tightened to the specified value with a torque wrench, and then the spherical nut should be tightened to the specified value.
Maintenance matters of the axle lubrication system:
1. The axle lubrication system is divided into grease lubrication system and oil lubrication system. It is recommended to use lubricating products suitable for different systems.
2. For the camshaft bushing and brake adjustment arm, add grease every three months until new grease overflows around the grease nozzle. Regular grease filling helps reduce mechanical hard wear.
3. After each removal of the wheel hub bearing, it is recommended that customers replace the new wheel hub seal ring to obtain safer sealing performance.
According to the appearance style and manufacturing process, the axle can be mainly divided into American axle and German axle. The main difference between the two is the shaft head.
(1) From the appearance point of view, the shaft head of the American axle is thicker, maintaining the basic shape of the shaft tube and the shape is relatively regular. The shaft head of the German axle is thinner, the shaft end is irregularly processed, and there are more bevels. Therefore, the axle head of the American axle is thicker, the part connected to the bearing is stronger, and the load it can bear is relatively larger.
(2) From the processing technology point of view, the American axle adopts an integrated axle body manufacturing process, that is, the axle heads at both ends are integrated with the axle tube in the middle, and they are directly polished from a steel tube. The axle heads at both ends of the German axle are welded to the axle body. During production, the axle body is the axle body and the axle head is the axle head. After production, they are welded together. From this perspective, the American axle does not have subsequent welding processing, and the original integrated axle has a stronger load-bearing capacity.
Customers choose the appropriate American axle or German axle according to their actual use needs. The more important work is to do a good job of maintenance during the later use process to improve the service life and safety performance of the axle.